Industrial air compressor types range widely, depending on the required application. These compressors provide a variety of functions from creating plastic bottles to providing breathing air in confined spaces.
In this article, you will learn about the different types of compressors, compressor accessories, and maintenance considerations.
Industrial Compressor Types
There are two major families of compressors: positive displacement compressors and dynamic displacement compressors. They are classified into these two groups by how the pressurization activity is performed. Positive displacement compressors increase air density by mechanically reducing the available area. Dynamic displacement compressors first increase air velocity and then reduce the available volume.
Positive Displacement Compressors
Positive displacement compressors operate by sucking in a volume of air, reducing the chamber size, and then exiting the air through an exhaust port. There are two main types of positive displacement compressors: reciprocating and rotary compressors.
Reciprocating Compressors
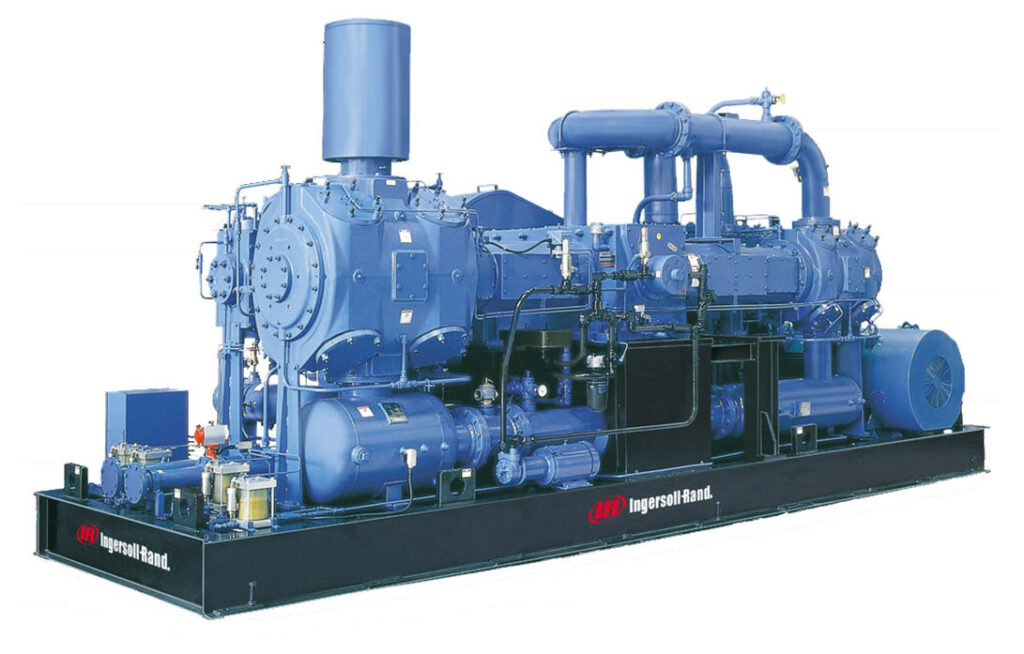
A piston-cylinder arrangement is at the heart of a reciprocating compressor. As the piston moves back and forth in the cylinder, it is in a reciprocating motion. Air is brought into the cylinder, compressed, and then exited. Inlet and outlet valves are sized and timed so that the compression cycle is optimized.
Reciprocating compressors are a good fit for low-volume, high-pressure applications. Small industrial compressors, often referred to as “shop compressors” are almost always reciprocating. Special reciprocating compressors are used in high-pressure applications. In such a scenario, a reciprocating compressor will have several stages and cooling between each stage. This allows high-pressure air to be delivered without damaging compressor internals.
Rotary Screw Compressors
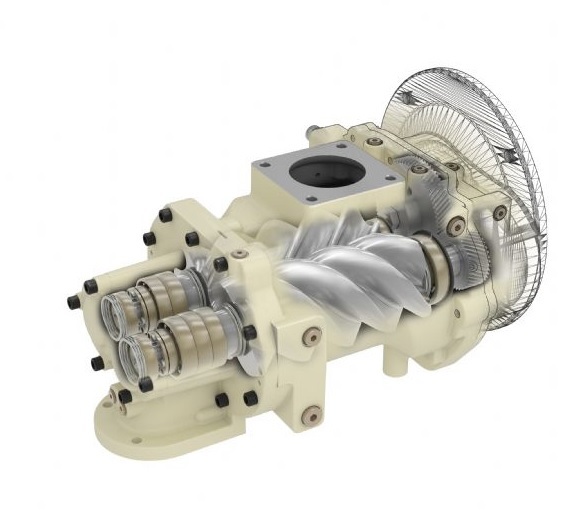
Two helical screws compress the air. These screws, sometimes called rotors, are classified as a female rotor and a male rotor and together are known as the airend. When both screws rotate, the air is continuously pushed to the other side. Thus, a vacuum is created between the rotors, sucking intake air inside. A good application of a rotary screw compressor is when the compressor is stationary and mid-range flow is required. Rotary screw compressors come in two different configurations: oil-flooded and oil-free.
Oil Flooded Screw
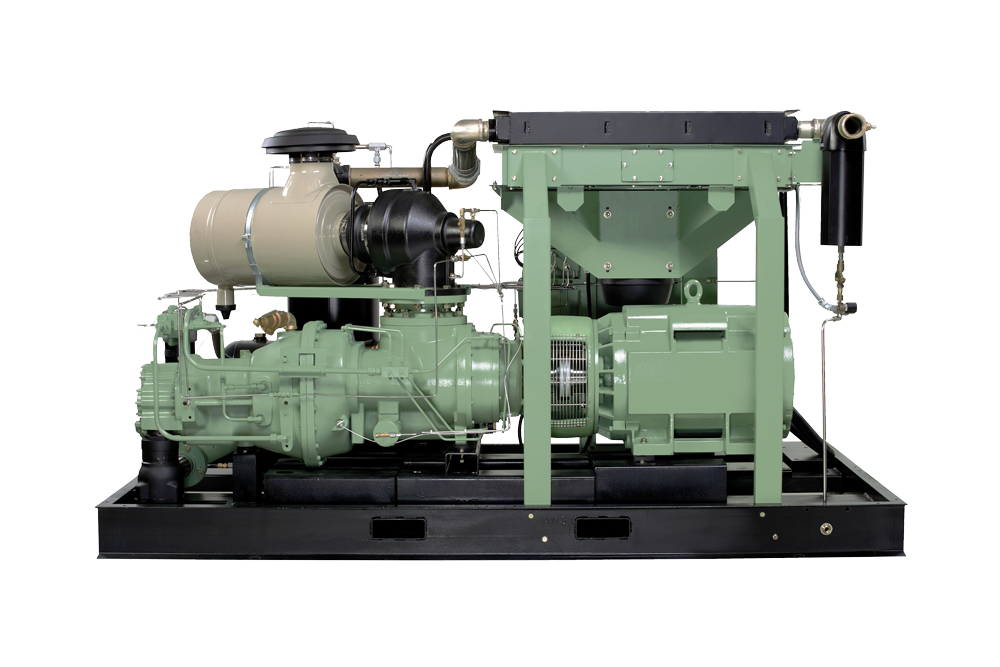
Oil flooded (also called oil-injected) compressors require oil lubrication. These are the most common types of screw compressors. Oil is injected in the chamber where compression takes place. Post compression, oil separators reduce hydrocarbons in the exhaust. No matter the degree of hydrocarbon separation at the outlet, oil-flooded compressors cannot be considered oil-free.
Oil-Free Screw
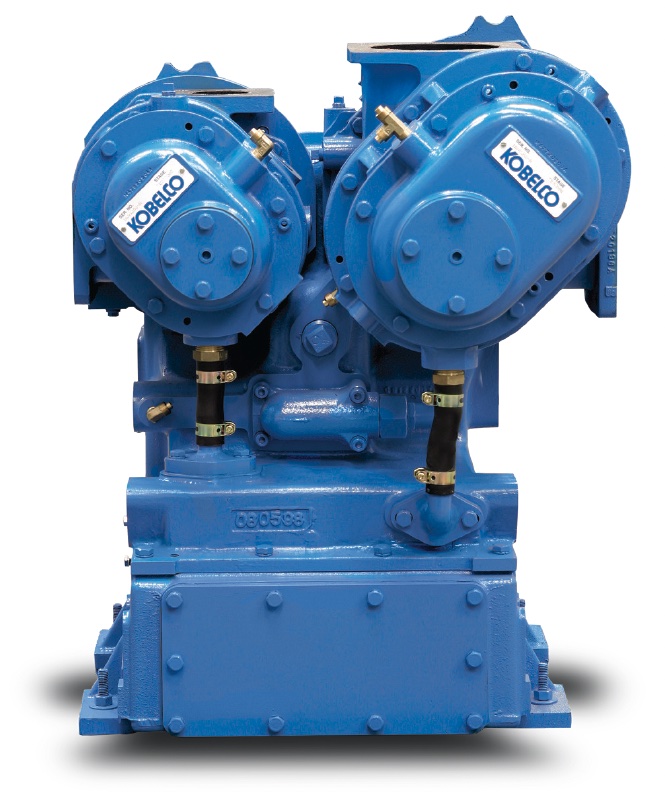
Oil is not required for the functioning of these compressors. High-quality rotors are used in the manufacturing of oil-free compressors. The rotors have very little space in between them and never touch each other to avoid the chance of damage. As there is no oil used, compression may be performed in stages to avoid overheating. Oil-free compressors are required in medical and food-grade applications.
Rotary Vane Compressors

The basic assembly of vane compressors includes a cylindrical rotor and a vertical slot that contains radial sliding vanes. The vanes are capable of an in-out motion. The vanes experience centrifugal force and are thrown outwards by the spinning motion of the rotor. The inlet air gets sucked in by these vanes and as the rotor continues to turn the volume of the trapped air is reduced and the pressure becomes higher.
Rotary vane compressors see the same mid-range applications as their screw counterparts. Rotary vane compressors cost more to produce but are more energy efficient, run at a lower speed, and require less maintenance than rotary screw compressors. As a result, rotary vane compressors can have a nearly unlimited operating life if properly managed.
Dynamic Displacement Compressors
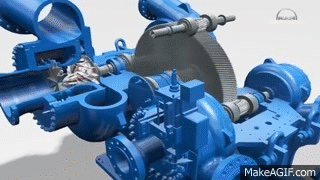
Dynamic displacement compressors work on a different operating principle than positive displacement compressors. These compressors first increase the air velocity and then restrict its motion, causing air pressure to increase. Dynamic displacement compressors are usually oil-free and broadly classified into two categories: axial compressors and centrifugal compressors.
Axial Compressors
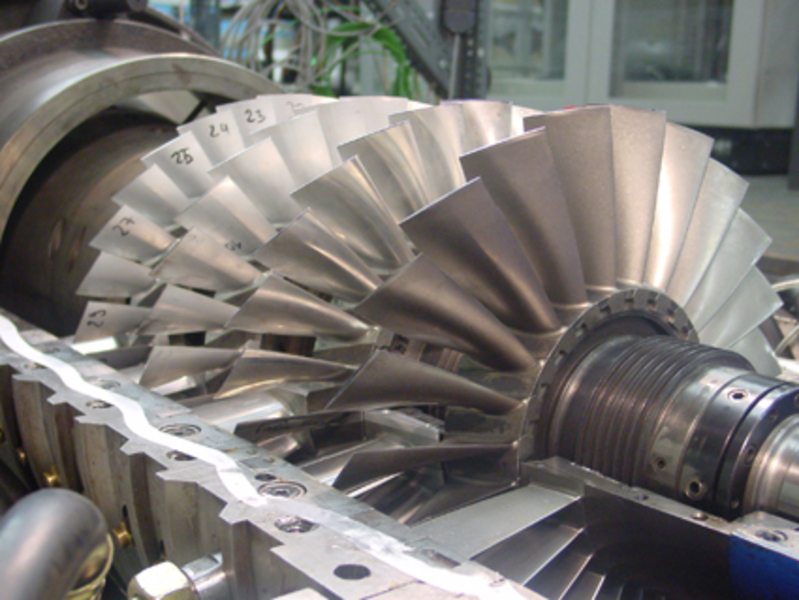
Axial Compressors consist of two main parts:
- Drum
- Blades
The blades are attached to the drum. The specific geometry of the blades plays an important part in the functionality. The direction of the gas at intake and exhaust are the same and most of the time this intake and exhaust occur in an axial direction. Axial compressors consist of multiple stages and each stage contains:
- Rotors– the set of rotating blades to accelerate the gas flow.
- Stators – the set of stationary blades that convert velocity to pressure.
Axial compressors are used as part of power-generating turbines and in large industrial applications such as blast furnaces and fluid catalytic cracking.
Integrally Geared Centrifugal Compressors

These compressors usually consist of multiple stages. Each stage consists of one rotating element and one stationary element. Centrifugal compressors intake the gas axially and discharge radially from the rotating element. The rotating element, also known as the impeller, induces kinetic energy in the gas molecules. Then the gas passes through the stationary element, the diffuser, where according to Bernoulli’s principle, velocity is converted to pressure. Centrifugal compressors are used in plants, facilities, and transport applications where high flow rates are required at relatively low pressure.
Specifying an Air Compressor
The key factors that are considered for selecting the right compressor for the task include:
- Flow rate required – The amount of flow required, usually expressed in cubic feet per minute. In metric applications, flow is typically expressed as “normal cubic metre” (Nm3). There are three types of flow rates commonly referenced in the compression industry.
- SCFM (standard cubic feet per minute)- This is the flow rate under standard pressure and temperature conditions (68°F and 36% relative humidity at sea level.)
- ACFM (actual cubic feet per minute) – This is the flow rate under actual site conditions.
- ICFM (inlet cubic feet per minute) – Typically used by compressor vendors, this measures flow in front of additional equipment like an inlet filter, blower or booster.
- Pressure required – Pressure is typically referenced in psi (pounds per square inch).
- Air quality – Oil-free air may be required.
- Average operating duty cycle – This tells a user how long the compressor is expected to run, typically expressed as a percentage of run time/overall time. Continuous duty cycles are the most demanding application.
Additionally, a user has to understand site conditions. The compressor will perform differently depending on where it is located. Four site conditions and their impact on compressor performance are as follows:
- Humidity – More moisture in the air leads to decreased flow.
- Altitude – As altitude increases, the air becomes thinner. This reduces airflow and air pressure.
- Air Inlet Temperature – As air temperature increases, airflow and pressure decrease.
- Coolant Temperature –Hotter cooling water reduces airflow and air pressure.
Due to their operating principle of using velocity to create pressure, dynamic displacement compressors are more susceptible to variations in site conditions than positive displacement compressors. As such a careful examination of the relationship between the flow and pressure is warranted.
The relationship between pressure and the flow rate is expressed in the form of a compressor curve. This curve informs the reader of the range of pressures and corresponding flows under which a compressor can operate. The lowest pressure point on the curve is called the choke point. The choke point is when the flow rate cannot physically increase. The highest pressure point is referred to as the surge point and notes where the flow becomes unstable and fluctuates dramatically.
Air Treatment & Accessories
Picking the right compressed air system for an application involves more than the compressor itself. The associated accessories, which ensure the compressor operates properly, are a key element of specifying a compressor system.
Aftercoolers
At higher pressures air temperature produce a significant amount of heat, requiring a mechanism to get rid of this waste heat energy. A cooler placed right after the compressor unit precipitates and partially condenses the gas in order to reduce the temperature. Most coolers are based on air cooling or water cooling. Some compressors also use oil cooling processes to dispose of the excess heat. Cooler systems are frequently integrated into the unit, but bigger units may have provisions for supplying cooling water on site.
Piping
Pipes must maintain the appropriate pressure in the system. Improperly sized or clogged piping systems can lead to compressor failures. The piping materials can be divided into two categories: non-metal and metal.
Non-metal Pipe
Typically, these are plastic pipes that are non-corrosive and lightweight, such as PVC. These types of pipes have temperature limitations and cannot be used in high-temperature vicinities. Plastic piping is generally considered to be commercial or specialty grade. Some compressor lubricants can break down the glue used to bond the pipe and fittings. Plastic pipe that is installed in direct sunlight may become brittle overtime and shatter if impacted. PVC under pressure will explode and send shrapnel like shards in every direction. There is a massive safety risk to using plastic or PVC piping in compressed air systems. The marginal material savings does not outweigh the potential serious safety risks. Don’t use it.
Rigid Pipe for Distribution System
Black iron, stainless steel, aluminum, and copper pipes fall into this category. These pipes are rated for higher-temperature applications. The specific type of metal pipe will depend on the application of the compressor (oil free or flooded) as well as the price positioning of the compressor. Consider overtime the heat and moisture present in a typical air stream will progressively corrode standard materials like black iron pipe. Over time this corrosion and foreign matter will buildup causing restrictions, blockages at low points (drains) and eventually affect end-devices. The cost to maintain filtration to protect against this extra corrosion will be multitudes higher than selecting a better piping material at installation.
Inlet Air Filtration
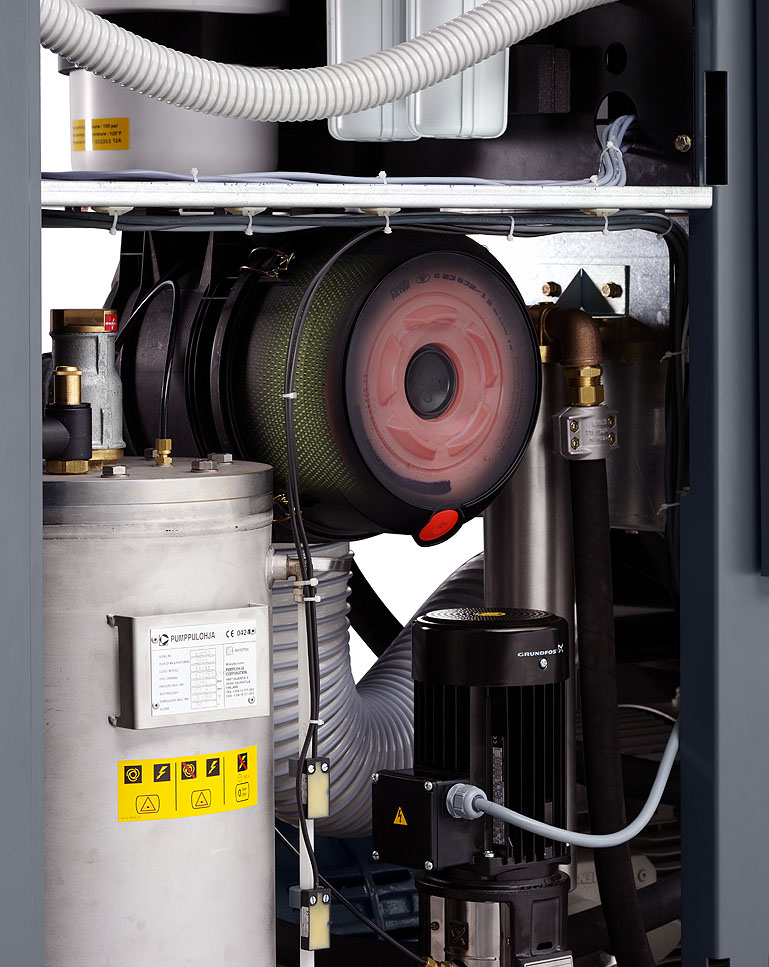
Filtration is grouped in two main categories: pre and post compression.
Pre-filtration can take on several forms including an exterior panel filter to catch large particles before entering the cabinet. All air compressors will have an inlet filtration system generally located near the inlet of the compressor flange before the first compression stage. A basic dry-type inlet filter will be standard and filter a normal load of airborne particulate. For high dust environments, a two-stage filter may be used to catch more fine particle as well as increase the surface of the filtration media to extend service intervals. Specialized filters such as ‘Absolute’ inlet filters are available for demanding applications o capture particulate 0.3micron and larger at a 99.97% efficiency rate. Chemical inlet filtration systems are available for compressors that will be ingesting noxious chemicals that would be damaging to a compressor if left untreated.

Post filtration can take on may forms as well. The main purpose for these filters is to remove any oil, water, and solids produced from compression or entrained from the piping to protect downstream air treatment components and end-devices. These filters are generally installed in-line with the piping and feature a removable element that is typically replaced based on a differential pressure value. Common classes for inline filters include particulate, coalescing, and activated carbon type and categorized based on the constituents they are designed to remove. Specialized filter systems are designed where will be used for human consumption such as SCUBA tanks, firefighting, and sandblast hoods. Small point of use (POU) filters may be installed directly ahead of sensitive equipment to ensure final level of protection against any contaminants from piping or a failed dryer/filter upstream. As a rule, the more filtration that is added to the system, the higher the operating cost and expense for ingoing maintenance. Filtration should be applied at to deliver a reasonable level of protection, but not more so that is required.
Coolant
An ideal coolant is any chemical substance, liquid or gas, with high thermal capacity and low viscosity. It is important for a coolant to not promote corrosion of the chambers they are used in to reduce temperature.
Dryer
Dryers are used to reduce the moisture content produced after the cooling procedure in air particles. Moisture creation in the unit is unavoidable so an efficient dryer is crucial to proper functioning. There are two types of dryers: refrigerated dryers and desiccant dryers.
Refrigerated Dryer

Refrigerated air dryers use a refrigeration compressor and subsequent heat exchanger to cool compressed air and remove moisture. Refrigerated dryers can be cycling and non-cycling. Cycling dryers turn on and off to deliver the correct amount of drying as needed. Non-cycling dryers do not have logic build into their operating behavior and run continuously. Cycling dryers require greater capital expense but have a lower operating expense.
Desiccant Dryer
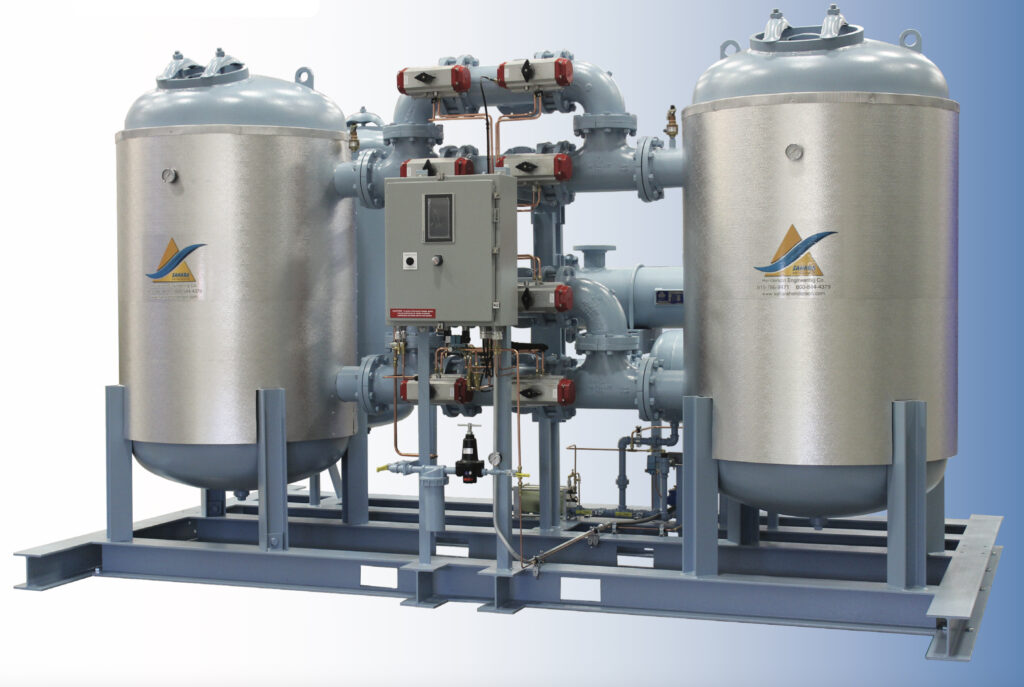
Desiccant dryers use absorbent material to collect moisture. Most desiccant dryers have two “beds” of absorbent material. As one bed is drying, the other is regenerating. Desiccant compressed air dryers are a good fit when the compressor requires very dry air. Desiccant dryers are typically a more expensive option than the refrigerated style.
Drain Valves

Air drains require regular drainage for efficient operation. Any presence of water particles may result in corrosion of the surface and low air pressures. Drain valves help drain any excess moisture present in the chambers.
Storage Tanks

The compressed air is stored in a specifically designed storage tank with the capability of removing water and cooling the air. The purpose is to maintain a steady air pressure by damping the pulsations caused by the discharge line of the compressor. Efficient storage tanks come with the ability to precipitate to remove the possible moisture and oil particles present inside the compressed air.
Storage tanks are classified as either wet or dry. Wet storage tanks are located before the air-drying unit. The air coming from the compressor enters the tank from the bottom port and exits for the top after being processed by the dryer. Dry storage tanks are present after the air-drying unit and store the processed air that is dry and filtered.
Air Compressor Controls

Control systems include various electrical controls, be it PLCs, HMIs, and switchboards. However, a controller ultimately ensures the proper and safe functioning of the compressor. It maintains the pressure inside the storage tanks using a pressure outlet valve. It uses different sensors to start, status, and modify the compressor’s behavior. Typically larger compressors will use a controller in the form of a HMI (Human-Machine Interface) on the compressor itself. When multiple compressors are installed a master system controller can be used to reduce power cost and maximize efficiency.
Remote Monitoring
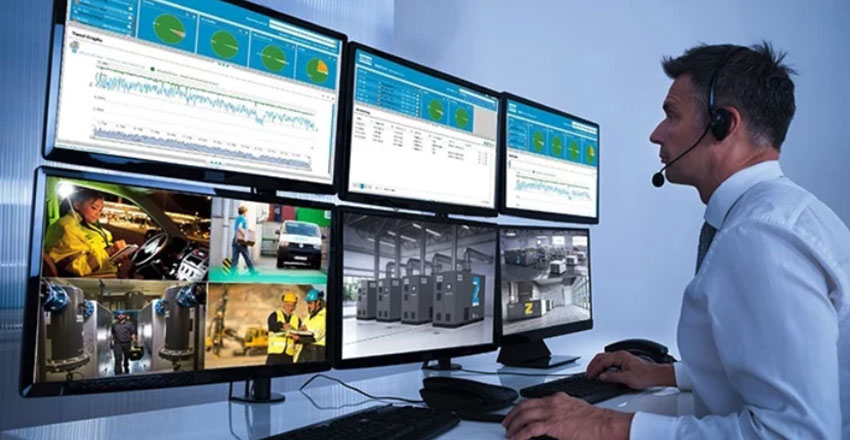
Remote monitoring allows for distant surveillance, and at times, control over the compressor’s operating behavior. This enables monitoring of a compressor’s activity and status by providing values such as temperature, pressure, and flow to ensure proper functionality. A software program is required to fetch sensor data and produce results on the basis of obtained values that can be displayed on computer screens.
Maintenance and Repair Considerations
Oil filters (if applicable), air filters, and oil/water separators must be changed at regular intervals to ensure proper performance. Routine maintenance inspections should include an overall audit of system performance as well as a multi-point inspection. Most manufacturers will recommend a prescribed preventive maintenance routine. This routine is typically required to keep the manufacturer’s warranty intact.
Oil sampling is a common testing process for an oil-flooded machine. Oil sampling allows the compressor owner to determine what contaminants are present in the atmosphere.
The extent of repairs tolerated depends on the capital cost of the unit. With the exception of multi-stage, high-pressure machines, many reciprocating compressors are replaced, rather than repaired, when serious internal damage is incurred. The airend of screw compressors is frequently overhauled, but this depends on the age and expected remaining service life of the compressor. Dynamic displacement compressors have the largest capital costs, making them prime candidates for extensive overhauls.